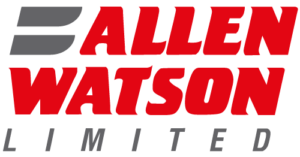
PIPE INSTALLATION BY GUIDED AUGER BORING | CASE STUDY
PROJECT CLIENT:
TENDRING DISTRICT COUNCIL
PIPE DIAMETER:
VARIOUS
MAIN CONTRACTOR:
JACKSON CIVILS LIMITED
PIPE MATERIAL:
SLOTTED AND SOLID HDPE
LOCATION:
HOLLAND ON SEA, ESSEX
PROJECT OVERVIEW
As part of a coastal cliff stabilisation contract 42no. land drains were required to reduce ground water collecting within the Kesgrave Sands & Gravels on top of the London Clay. The water bearing sands and gravels were highly unstable and could not be exposed in an open excavation without immediate collapse. The presence of this unstable, water-bearing ground in this almost inaccessible location behind and below the promenade significantly affects slope stability and a specialist method of drain installation was necessary.
DESCRIPTION OF WORKS
Allen Watson Ltd determined that with a small horizontal directional drilling rig modified to work at a very steep angle could drill from the upper promenade and steer a curved profile to arrive at a suitable level to tie in to a collector drain beneath the lower promenade. The entry position at the upper promenade would be in dry Kesgrave Formation and the lower promenade excavation would be in stiff London Clay which could support a stable excavation.
A second innovation was required to install the fragile, slotted screen with geotextile wrapping into correct location without damage. The geotextile wrapping was so flimsy it could not be dragged through the ground at all without risk of damage so the method devised involved pulling a carrier sleeve into the pilot hole in a conventional HDD manner with the delicate, wrapped screen pre-loaded inside. Once at the drilling rig the head of the carrier sleeve was disconnected and the end of the wrapped screen then securely anchored. The carrier sleeve meanwhile was attached to an excavator at the lower (opposite) end of the drilled hole and, once the instruction was given, the sleeve was pulled out of the hole.
Using the described method, the wrapped screen assembly was only ever moved against the smooth internal bore of the carrier sleeve and never against the rough and unstable sands and gravels. The carrier sleeve could be reused multiple times.
Initially 160mm slotted and wrapped screens were installed inside 200mm SDR11 carrier sleeves. The client determined that a smaller screen would deliver sufficient ground water flow so smaller 50mm screens were installed within 90mm carrier sleeves for the remainder of the bores. In total 42no. drains were installed along a 400m stretch of coast line.
REFINING THE METHOD TO PREVENT FAILURES
Early on in the works, and despite all the above described precautions, occasionally the running sand and gravel flowed into the carrier sleeve as it was being extracted resulting in damage to the weak slotted screens. Once the cause of the problem was determined Allen Watson Ltd realised that the solution was to find a way of blocking the annulus to the materials which could potentially flow in. AWL successfully developed a process of surcharging the annulus with biodegradable drilling fluid while the extraction was executed. From this point onwards the installations were 100% successful and all filter screens passed the required function tests.
POTENTIAL FURTHER USES OF THIS INNOVATION
The same method can be applied to pipes of various sizes and materials. Any situation where a perforated screen is needed in a difficult location could be considered and applications including but not limited to; groundwater extraction for slope stability, ground engineering or water supply, water injection for ground water recharge or soak-away, contaminant extraction for ground pollution remediations, and land fill or natural gas extraction for commercial use.
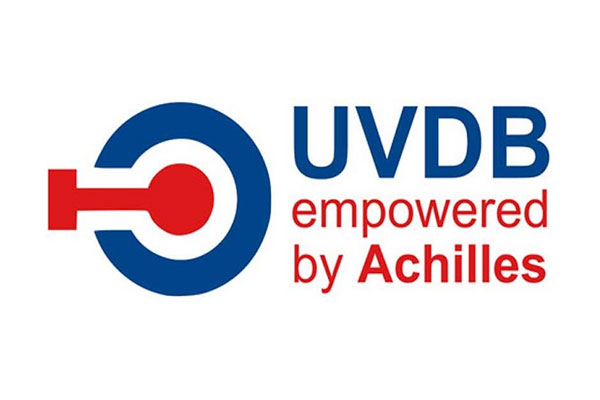
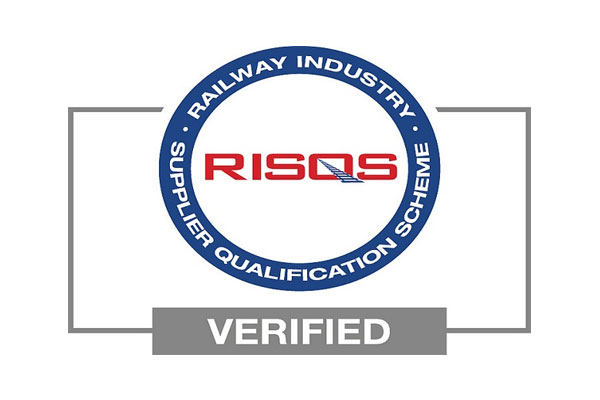
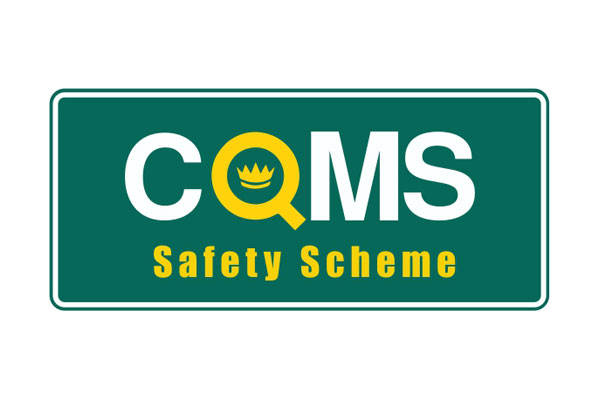
allenwatson.com