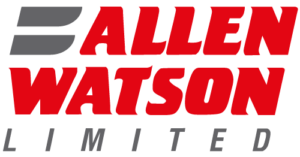
DN300 VITRIFIED CLAY PIPES INSTALLED ON A VERY DEMANDING SCHEME | CASE STUDY
PROJECT CLIENT:
eight2O
PIPE DIAMETER:
DN300
GROUND CONDITIONS:
HOMOGENOUS CHALK & FLINT PARTICLES
PIPE MATERIAL:
VITRIFIED CLAY
INSTALLATION MACHINE:
GAB85V GUIDED AUGER BORE WITH OPTICAL GUIDANCE SYSTEM
PROJECT OVERVIEW
The Works form part of the construction of a run to waste pipeline between the Marlborough WTW and a new soakaway borehole. Included in the works is a 54-metre section which crosses under the CLH fuel pipeline (CLH-PS). All works including the construction of shafts, and the installation of the pipeline’s connection of the pipeline in the shaft and the reinstatement of the excavated ground was to be undertaken by a sole contractor.
DESCRIPTION OF WORKS
To qualify for the project AWL had to meet the specifications with regard to the strict SH&W and Environmental requirements of the eight2O Orientation and Thames Water Passport. This included having all persons fully CPCS certified for the activities they were to undertake, all operators need to undertake a full medical.
The senior AWL supervisor was required to be qualified to undertake the duties of a Front Line Supervisor, who can demonstrate that they have the necessary knowledge and skills to supervise their workers effectively. This is essential las they are to ensure those under their control carry out their tasks with due regard for the SH&W of themselves and others.
Allen Watson /Cappagh Construction JV was formed to meet the contract specification of the project being undertaken by a sole contractor. It was agreed that Cappagh Construction would undertake the construction of the drive and exit shafts and after pipe installation couple the pipelines together and back fill the excavations. AWL was to undertake all the auger boring tasks.
Cappagh Construction constructed the first 2.4 metre caisson shaft at a depth of 4 metres which was to be used as a drive shaft for a 74-metre drive before rotating the GAB machine and installing a 24-metre drive from the same caisson shaft. The reception shafts were constructed by eight2O which consisted of a 3 metre trench box with road plates at the front and back of the box.
AWL installed the Naylor Denlok DN300 NC jacking pipes by the means of its GAB 85 guided auger boring machine. As the ground conditions changed to chalk with a high level of flint, water was needed to be added during the auger process increasing the rotary torgue due to the chalk deposits on the auger flights.
As installation progressed the full 18,000Nm of rotary torque which is available on the AWL GAB 85 machine was required, to rotate the flight augers in the hard ground encounted.
Following installation, the pipelines were connected in the drive shaft and fully tested in accordance with EN610.
The third pipeline required installation from a 2.4 metre caisson shaft at a depth of 4 metres which was required to pass beneath a CLH-PS fuel pipeline. To ensure that the ground movement beneath the CLH-PS pipeline was inside the acceptable limits the pipeline had to be exposed and monitored by authorised personal while the installation of the jacking pipes took place.
Following the installation of the jacking pipes the CLH-PS pipeline was reinstated under supervision.
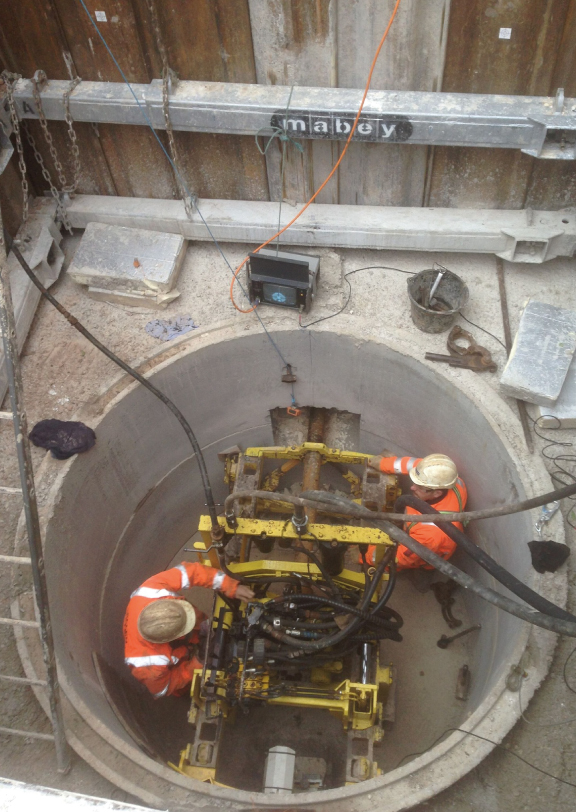
CLIENTS REMARKS

AWL is a competent contractor who have great experience in GAB works which can be seen first-hand from their management right the way through to their project team working on-site. Both Management and Workforce at AWL have a co-operative approach to working with the Client, which made working with AWL a very rewarding experience on a very demanding scheme, I look forward to working with them again in the future.
James Reapy
eight 2O Site Agent
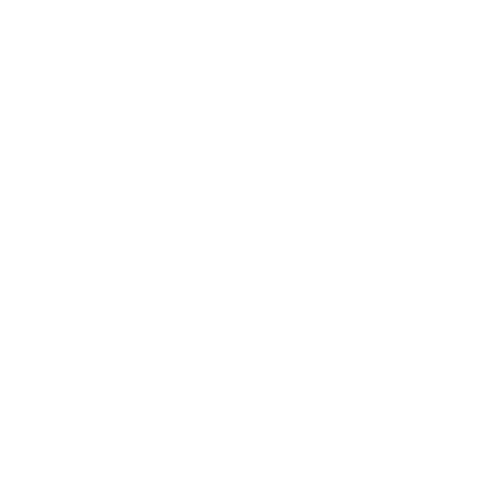
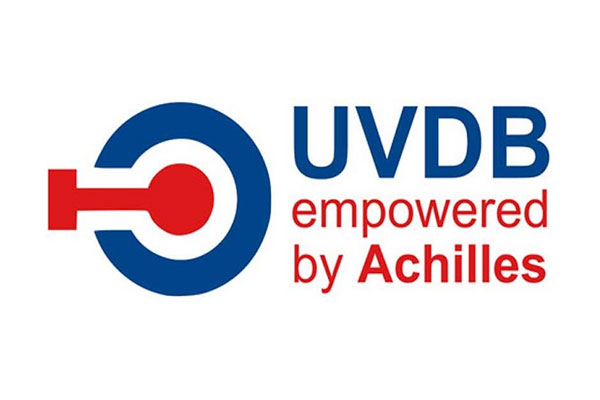
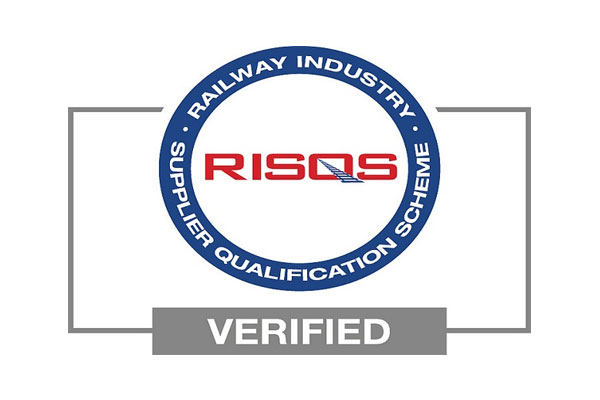
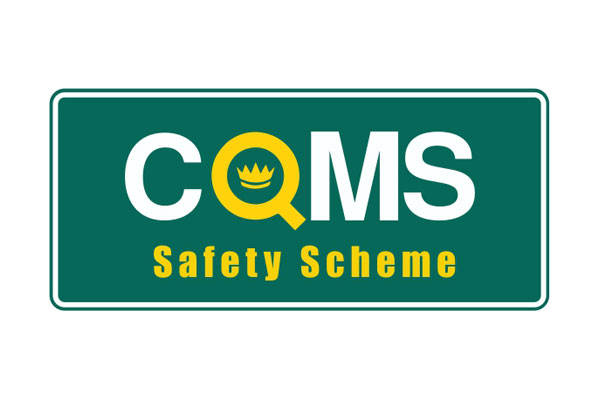
allenwatson.com